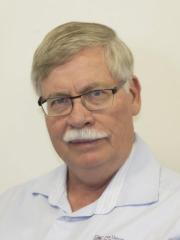
Dr Rob Morrison's research focused on achieving a better understanding of mineral processing and ways to use insights gained to identify potential possibilities for improvement, new flow sheets and equipment.
Rob's technical interests include energy efficient mineral processing, advanced sorting techniques, characterisation of liberation and breakage, simulation and measurement techniques. Rob has published more than 200 technical papers, contributed to several text books and holds several patents.
Rob Morrison is a metallurgical engineer with more than thirty years of experience in mineral processing. His experience includes operations and process development during four years at Bougainville Copper and plant design, construction and commissioning during six years with Fluor Daniel Australia.
For nine years Rob was Manager of JKTech which provides optimisation and control services to the mineral industry as well as ore characterisation and the JKSimMet range of user friendly simulation software. He developed in collaboration with AMDEL the Dry Stream Analyser which is marketed by ThermoGamma Metrics with Tim Napier-Munn. He set up and managed the project which led to the development of the Mineral Liberation Analyser by Dr Ying Gu. For the initial two years of its operation, Rob was the leader of Program 2 of the Centre for Sustainable Resource Processing. Program 2 focussed on improving the eco-efficiency of existing operations. Rob was the leader of AMIRA Project P754 which developed a Code of Practise and a text book for Metal Accounting. Rob was also a founder member and a major contributor to the Rio Tinto Centre for Advanced Mineral Separation. More recently, he has been working on the Next Generation project funded by METSO.
Industry
Rob has been engaged with industry, through consulting and research projects for more than 30 years. He has helped to develop new software, instruments and equipment in projects with mining companies and equipment suppliers.
Collaborations
Rob’s major collaborations include, the Centre for Sustainable Resource Processing, various AMIRA projects including JKSimFloat, the Mineral Sands project, the Metal Accounting Project and P9.
However, his most satisfying collaboration has been working with Dr Paul Cleary of CSIRO. This 15 year collaboration has generated more than 30 published papers and has made a major contribution to a more detailed understanding of the processes of mineral processing.
Key Publications
Pokrajcic, Zeljka, Morrison, Rob and Johnson, Bill (2009). Designing for a reduced carbon footprint at Greenfield and operating comminution plants. In: D.Malhotra, P. R. Taylor, E. Spiller and M. LeVier, Recent Advances in Mineral Processing Plant Design. Mineral Processing Plant Design - An update 2009 Conference, Tucson, Arizona, U.S.A., (560-570). 30 September - 3 October, 2009
Morrison, R. D. and Gaylard, P. G. (2008). Applying the AMIRA P754 code of practice for metal accounting. In: MetPlant 2008, Metallurgical Plant Design and Operating Strategies, Proceedings. MetPlant 2008, Perth WA, (3-17). 18-19 August, 2008.
Morrison, R. D. and Cleary, P. W. (2008). Towards a virtual comminution machine. Minerals Engineering, Volume 21, Issue 11, October 2008, Pages 770-781
Cleary, P. W., Sinnott, M. D., Morrison, R. D., Cummins, S. and Delaney, G. W. (2017) Analysis of cone crusher performance with changes in material properties and operating conditions using DEM. Minerals Engineering, 100 49-70. doi:10.1016/j.mineng.2016.10.005
R.D. Morrison, B.A. Adair, S. Walters and S. Gray. (2017) Comminution devices for more sustainable processing. Physical Separation 2017, Falmouth Cornwall
Funding
At the time of moving to JKMRC, JKTech was earning approximately $3M per year.
CSRP funding amounted to approximately $1M per year for 6 years.
CAMS received some $22m over approximately 6 years.
The Next Generation project has earned approximately $1M over 3 years