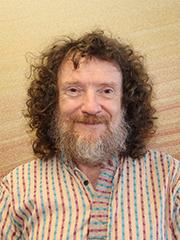
Measurement and modelling of the ore properties and comminution processes required to liberate minerals for optimal recovery.
Malcolm aims to link fundamental research into applied outputs through the development of mechanistically correct but practical and robust process models. He has conducted applied surveying and site optimisation studies on over 60 plants worldwide. Interests cover mill liner design, SAG mill modelling and control, the unified comminution model (UCM), ore characterisation for multi-component modelling, and Flexible circuits - to utilise today’s equipment while enabling the uptake of tomorrows technology. These are published in over 170 articles.
His research vision is of integrated total process simulation as a tool for innovation – linking geology, mining, energy and size reduction, gangue rejection and recovery into flexible process design and process optimisation.
After training in physics, from 1984, Malcolm developed mineral processing knowledge and research skills at Mintek (Council for Mineral Technology in South Africa) while completing an MSc and PhD. in 1994 he started his own specialist company (Liner Design Services) based on his research outcomes, then in 1997 formed the comminution research group at the University of Cape Town (UCT) and started the MPTech consulting group. Since being recruited to the JKMRC as the Chair in sustainable comminution in 2007 he has redeveloped the comminution group, founded the Anglo American Centre for Sustainable Comminution and formed the Global Comminution Collaborative (GCC) of six University world-leading groups providing a comprehensive worldwide process optimisation team.
Fellow AusIMM and SAIMM.
Awards: Medals for “Outstanding contribution to SAG and AG milling technology” at the 5 yearly SAG conference, 2001, 2006.
2006 Peterson Award, Society of Experimental Mechanics - Best Applications Paper published over a two-year period
The South African Institute of Tribology prize for "Best Technical Achievement" for work on liner materials testing.
3 outstanding paper and author awards for students at AusIMM and IMPC conferences.
Vice Chancellor’s Commendation for Internationalisation – 2014 for the Global Comminution Collaborative.
Industry
The industrial impact of Malcolm's research outputs is indicated in application to improving the operation of a wide range of industrial operations through over 60 comminution plant surveys, 35 mill liner designs, 20 grate discharge designs, 12 comminution plant designs and 35 comminution plant optimisations. His MillTraj liner design software has over 200 licences used by over half the mill liner suppliers worldwide to improve the milling efficiency of hundreds of mills.
The application of Malcolm's research to cross-disciplinary projects is often commented on by peers worldwide at conferences. He is called on by the major mining companies on 5 continents: such as Anglo American (Platinum, Base metals, Brazil), Anglo Gold Ashanti, Impala Platinum, Lonmin Platinum, DeBeers, Rio Tinto, BHP Billiton, Newcrest, Vale, LKAB, First Quantum Minerals, Barrick – to conduct research and process improvement work. Process improvement work has resulted in increases in throughput of up to 20%, valued at up to $100M per annum on a single plant.
Collaborations
Malcolm's global vision is exemplified in founding the Global Comminution Collaborative (GCC) in 2011. This unique group works as an extended network of researchers sharing projects, funding, students and outcomes to bring significant capability to the global minerals industry.
GCC members: JKMRC, University of Queensland; University of Cape Town (South Africa); Chalmers University of technology (Sweden); University of Braunschweig (Germany); Hacettepe University (Turkey); Federal University of Rio de Janeiro (Brazil).
Malcolm has researched in, led the comminution theme and become Project Leader of the international AMIRA P9 project (valued at round $13M per 4 year phase) over the past 18 years – working closely with 8 different University groups around the world and over 30 different sponsoring companies.
Key Publications
Ballantyne, G.R., Peukert, W. and Powell, M.S., 2014. Size Specific Energy (SSE) – Energy Required to Generate Minus 75 Micron Material. International Journal of Mineral Processing, vol. 139, pp. 2-6.
This paper expresses a rigorous approach to understanding energy utilisation, that my new researcher applied along with a world-leader in the modelling of fine particle breakage.
Powell, M.S. and Mainza, A.N., Step change – A staircase rather than a giant leap 2012. XXVI IMPC. New Delhi, India, 24-28 September, 2012: p. 2750-2760.
This thought leadership paper was presented at the IMPC as a keynote targeted at challenging the perspective of researchers and industry as to how to take up technology improvements.
Powell, M.S. and Bye, A.R. (2009). Beyond Mine-to-Mill – Circuit Design for Energy Efficient Resource Utilisation, Proceedings Tenth Mill Operators’ Conference 2009, 12 - 14 October, Adelaide, South Australia. The Australasian Institute of Mining and Metallurgy, Publication Series No 11/2009, ISBN 978 1 921522 12 3. pp. 357-364.
This launched the flexible circuit design concept, “FlexiCircuits”, attracting industry attention and forming a key aspect of the successful CRCORE bid, this presents the big picture of our research objectives.
Powell, M.S., Smit, I., Radziszewski, P., Cleary, P., Rattray, B., Eriksson, K., Schaeffer, L. (2006). The Selection and Design of Mill Liners, In Advances in Comminution, Ed. S.K. Kawatra. ISBN-13: 978-0-87335-246-8, Society for Mining, metallurgy, and exploration, Inc., Colorado, USA. pp. 331-376.
This is the most comprehensive published overview of mill liner design, covering the theory and application over the range of liner types and mills.
Powell, M.S., van der Westhuizen, A.P., and Mainza, A.N., (2009). Applying grindcurves to mill operation and optimisation, Minerals Engineering, Vol. 22, pp. 625–632. doi:10.1016/j.mineng.2009.01.008
A comprehensive description of the theory and application of my “Grindcurves” methodology used for selecting the optimum operating condition for large SAG mills, leading the application into industry.
Funding
Principal funding is from industry, but Malcolm has also had substantial Government grant funding.
He is the founding Director of the Anglo American centre for Sustainable Comminution, which has a 5-year contracted funding of $5 million, plus additional site work of about $1.5M. Additionally leveraged 1.5M UQ strategic funding off this Centre.
He was a programme leader in two CRC’s – CSRP and CRC ORE - programme funding of $0.5 to 1 M per annum over 7 years
Project Leader for the $13M AMIRA P9P project (2015 - 16), comminution programme leader in P9 projects over 12 years, about $3M per annum budget.
Director of the $2.1 M Metso VTM collaborative research
Developed and led a number of smaller industry funded projects and contract research jobs.