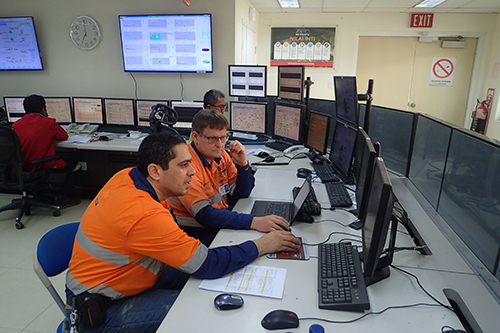
Researchers from the Sustainable Minerals Institute’s Julius Kruttschnitt Mineral Research Centre (JKMRC) are developing a soft sensor to overcome previously-accepted performance challenges facing Semi-Autogenous Grinding (SAG) mills.
SAG mills are a key asset for mineral processing operations as one of the critical stages of extracting mineral out of ore, and their continued stable operation is central to productivity.
However, the performance of a SAG mill changes rapidly in response to conditions such as feed size and hardness as well as longer-term variability due to liner wear – something no instrumentation can directly observe.
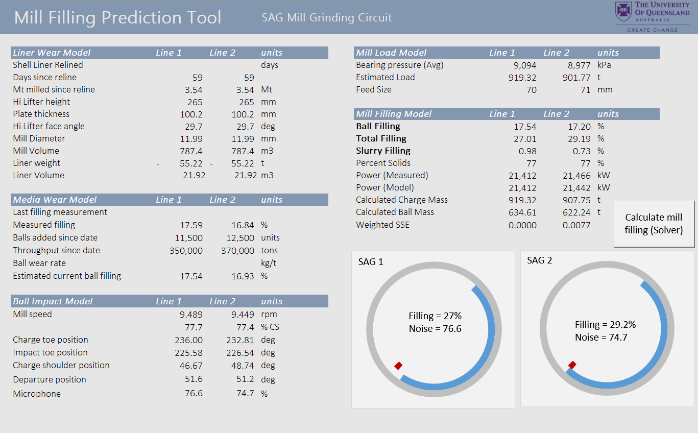
The new Mill Filling Prediction (MFP) tool is a soft sensor (a mathematical model that act as a sensor) to provide information about the mill’s contents and enable it to be controlled closer to its maximum capacity. The MFP tool is developed by Dr Marko Hilden, a Senior Researcher at JKMRC. He transformed and updated models that have been developed by various researchers at JKMRC and developed new models to suit the new application.
Associate Professor Mohsen Yahyaei who is JKMRC’s Advanced Process Prediction and Control (APPCo) Group Leader said the MFP tool includes mathematical models that predict the wear condition of the mill, the level of mill filling, the filling of the steel grinding media and particle trajectory.
“The models capture data from commonly installed sensors around SAG mills, which allows the model to run in real time, giving the operator instant feedback on the critical conditions that affect mill performance,” he said.
“The MFPT is already being implemented at a number of industrial sites, and they are starting to see multiple benefits in the control of the grinding circuit.”
In the mining sector, most energy is used during mineral processing, with comminution – which includes grinding – accounting for 70% of total energy usage in some sub-sectors.
Associate Professor Yahyaei said precisely predicting mill filling can increase operators’ confidence in running the mill at a higher average filling and power draw, thereby increasing overall equipment effectiveness and throughput.
“The operator can be alerted when undesirable conditions such as slurry pooling are imminent, reducing the risk of the mill being overloaded.
"Estimation and display of steel ball level reduces the need to perform regular manual measurements which require stopping and sometimes entering the mill, and therefore reduces impact on production and personnel health and safety.
“And warnings, when shell impacts are likely, can help the operators select operating conditions that avoid excessive liner wear and grinding media consumption.
JKMRC’s Advanced Process Prediction and Control Group aims to transform unit process modelling and simulation by moving from steady-state models to techniques that make greater use of data generated on-site and sensor technologies in combination with advanced process control, computational analytics and modelling techniques.
Contact: Associate Professor Mohsen Yahyaei, m.yahyaei@uq.edu.au